SHOP TALK: No Place Like Home
- JT
- Mar 11, 2017
- 6 min read
Updated: Oct 30, 2020
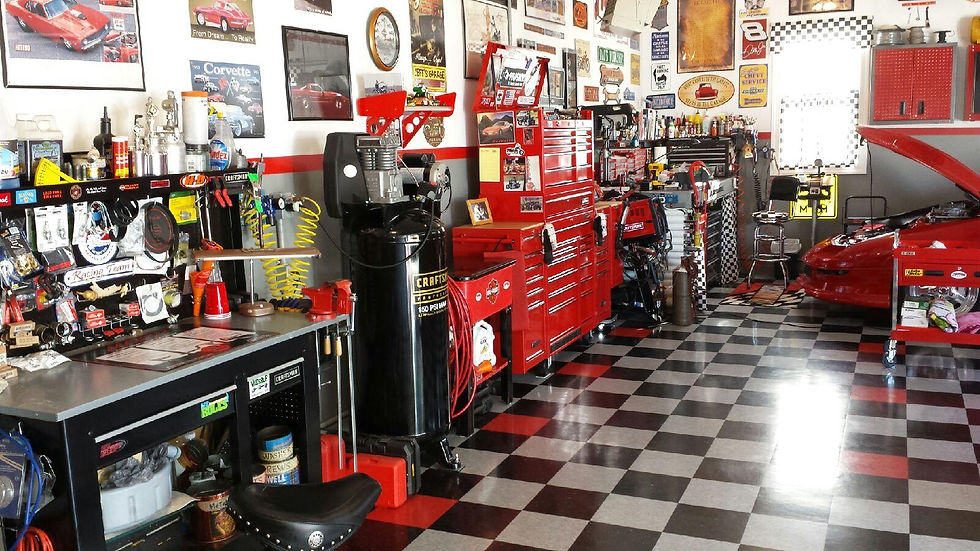
This past month I’ve been traveling quite a bit to work on cars outside of my home shop. It’s no secret that I’m an obsessive-compulsive, anal detail freak, who has an out-of-control tool addiction. Throughout my travels, I’ve visited and worked in shops of all shapes and sizes and surprisingly found they all have one thing in common.
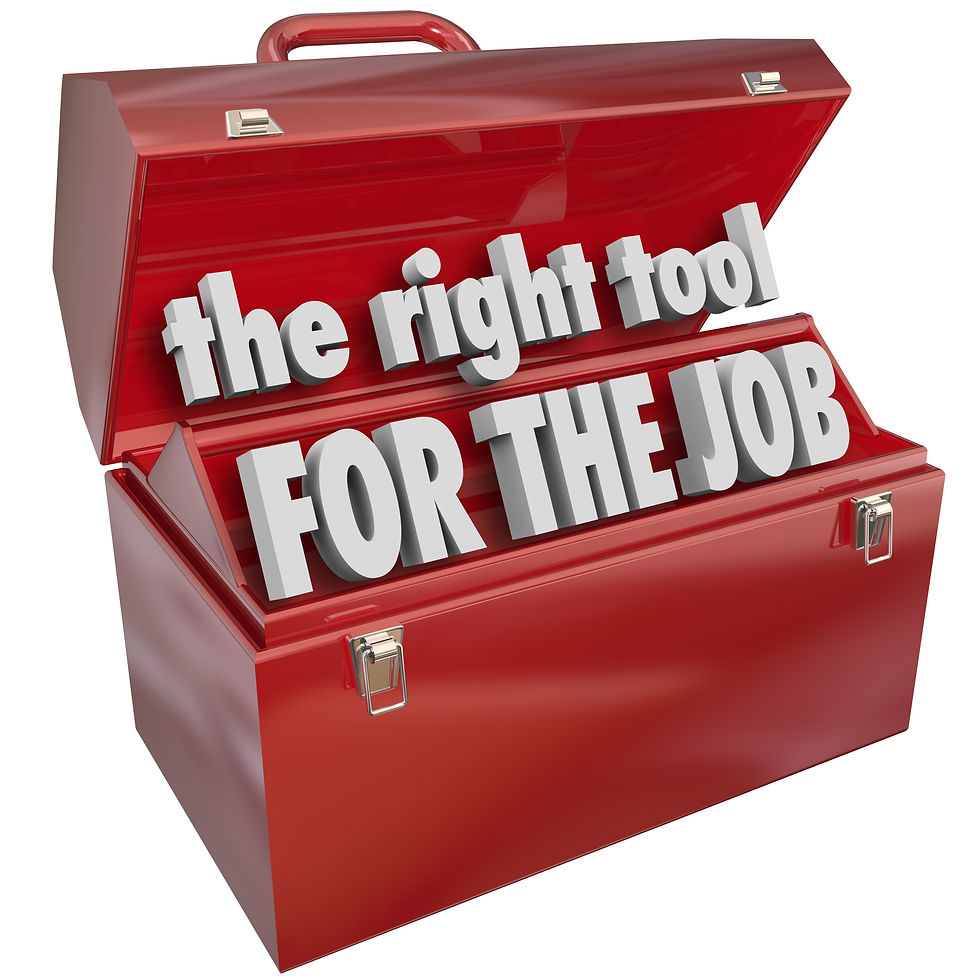
Whether it’s a small shop in a home garage, a full-time commercial one, or a multi-millionaires dream garage loaded with an amazing car collection, they all lack the proper tools needed to complete the job correctly, and I find myself wishing I was back home in my small, but very well-stocked shop.
I recently encountered this tool-deficiency epidemic while working on a repair in a garage that was easily twice as big as my entire house. To protect the guilty and keep my customers in the process, I will refer to him as Mr. X. Through a mutual acquaintance, Mr. X heard about my electrical skills and asked if I would travel out of state to work on his car. Time is money, and he was willing to pay my labor rate while traveling, so I agreed to take the trip and repair what several people had attempted to fix unsuccessfully. Mr. X assured me he had every tool I would need and kept reminding me he was a great mechanic but just lacked electrical skills.
When I arrived at his home, I was surprised to find an enormous detached, six-car garage at the end of his driveway. Once inside, I was impressed to see over a half million dollars worth of cars in his collection. It didn’t take long for my eyes to notice his toolbox. Mr. X had a small, 24-inch wide toolbox with five drawers on top and five drawers on the bottom. How could he possibly have EVERY tool I would ever need? My electrical toolbox is bigger than his entire tool collection. Yes, I admit I have a serious tool problem. Since I was hired for an electrical job, I remained optimistic and rolled up my sleeves to figure out what others could not.
After a quick diagnosis, it was apparent the entire electrical work on this near six figure car was done by a rookie. There were no solder connections, wrong gauge wires, no relays in high amperage circuits, and poor grounding. To add insult to injury, Mr. X didn’t want me to fix anything other than what I was hired to do.
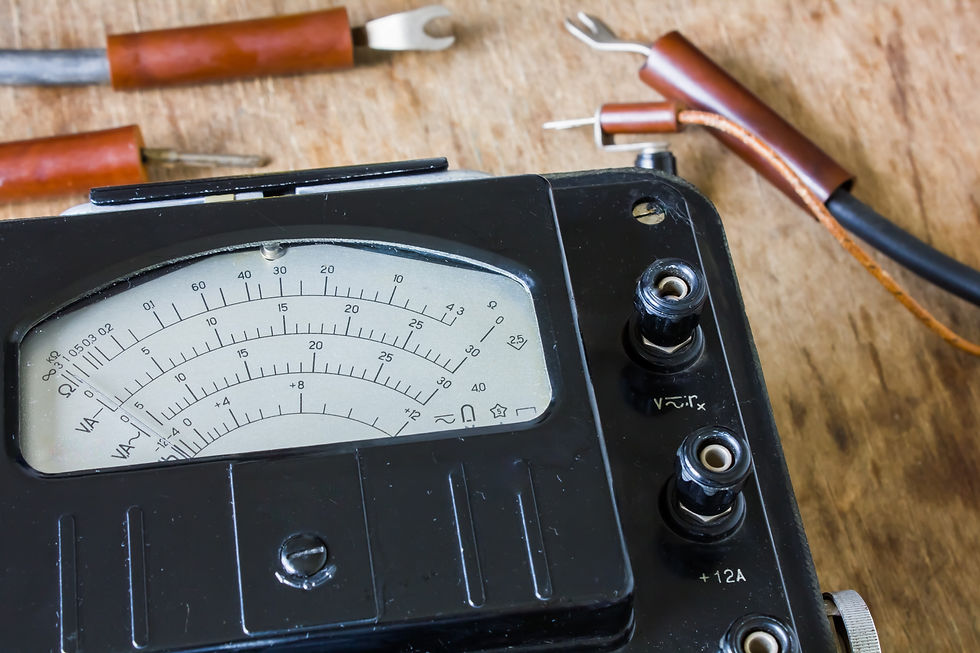
I asked Mr. X if he had a multi-meter and a test light. He handed me a piece of automotive memorabilia from the 70s that in its day was considered a multi-meter. He also handed me a very cheap looking test light from the same era. I opted to begin my diagnosis with the test light and after a few minutes of not finding any working circuits, I hooked the test light directly to the battery and discovered it was broken. I took a deep breath and grabbed the relic of a multi-meter. Believe it or not it took a few minutes of playing with it just to figure it out, but once I did, it didn’t take long to diagnose what the problem was – even with a 1970 multi-meter! Lucky for me, there was an auto parts store minutes from his house and after picking up some wire, a few circuit breakers, relays, a terminal strip, and a slice of pizza on the way home, I was ready to get to work (or at least I thought I was).

I asked Mr. X if he had a soldering gun and some solder. Surprise…his soldering gun didn’t work, but he had a soldering iron, which I actually prefer. The tip on the iron was a small pointed one. I had some 10 gauge circuits to solder and asked if he had some other tips for me to choose from. His response was, "I have soldered for over 20 years and this works fine." Once again, I asked if he had any other tips for me to choose from, and he informed me there is no such thing. I took the opportunity to educate him on what the small screw on the side of the iron tip was used for, unscrewed it and pulled the tip out. I then explained there are several different tips that could be inserted in the iron for different jobs. The 10 gauge wire I was working with needed the largest, flat edged tip. The small tip he had was so small that the 10 gauge wire actually acted as a heat soak and would not even melt the solder. I’d either be forced to use crimp connectors or send him to the store to buy a new soldering iron. Believe it or not, he chose the first option. Needless to say, his selection of crimp connectors and his actual crimper was far from ideal, but by the end of the day, I was able to fix his car.
Mr. X was elated, even though I told him his car would have never left my shop in its current condition. In addition to his lack of appreciation for me fixing the dozen other items that really needed attention, his poor tools made the work take nearly twice as long, and the results far from the standard of excellence I pride myself on. Before I left, I gave Mr. X a detailed list of tools and hardware that he should have in his shop to make his life, and the lives of those who help him, a lot easier. He was thankful and hopefully learned a valuable lesson.
Later that week, I was hired for another out-of-state job, and once again found myself in a tool-deficient shop (as I mentioned earlier, it is a widespread epidemic affecting a very large part of the gearhead community). I was hired by Mr. Z to fix an air bag problem on a resto-mod he was trying to get on the show circuit. Naturally, he assured me he would have every tool I needed to complete the job. Having learned my lesson earlier that week, I would have brought some of my own tools that were relevant to the job, but since I was traveling by plane, it was not an option. Upon arrival, I was blown away with Mr. Z’s shop. There was no shortage of amazing cars but the tools were far from amazing. I needed a few flare wrenches, air tools or an impact gun, a pickle fork, a real vise, a stubby combination wrench, a magnetic end for my sockets, and I would have loved my pressure/vacuum gauge with all of the necessary adapters I have accumulated over the years. Was I able to fix the problem with the air bags? Yes. Did it take ridiculously long and give me a headache in the process? Yes!

Now in the spirit of being fair, I have been hired by a few shops that share my level of passion for excellence or as some people call it, OCD. I have even seen and used tools that I never knew existed and immediately added them to my wish list. I firmly believe there is a tool for every job and make it a point to either buy or fabricate the tools that I’ve needed over the years.
Some people have their favorite cozy chair, some people have their custom made bed, and some people have a gourmet kitchen that enables them to cook and entertain. For me, my shop is my ultimate sanctuary. Every one of my tools is kept in a very specific spot in my shop and gets cleaned after every use. I do my best to keep my mini hardware store well stocked with nuts, bolts, washers, cotter pins, screws, keyways, o-rings, fuses, grommets, wire, and an assortment of steel and aluminum and everything else in between. I have also been spoiled by my oversized air compressor, air tools, mig welder, oxy/acetlyene torch, chop saw, grinders, wire wheel, lift, drill press, 20 ton press, overhead hoist, metal brake, drain pans, drop lights, magnetic lights, creeper, bead breaker, bead setter, spring compressors, TPMS Reset Tool, lap top, and the extra pair of hands from my daughter. My shop is filled with all of the tools and supplies I need to wrench away the stresses of life.
I would like to say that I am done with performing out of state repairs, but I love the challenge of fixing something that others can not. I also love the comradery of other gearheads. And I love having extra money to buy more tools for my shop and go-fast parts for my car. Despite my past experiences, I will continue to leave my comfort zone and help a gearhead in need. I am certain though that no matter where my travels take me, there truly is no place like home.
Keep wrenching,
JT