SHOP TALK: It's Just A Mud Truck!
- 908 Motorsports Magazine
- Jan 23, 2021
- 8 min read
This amazing and beautiful machine was created by two brothers. They went completely over the top making everything imaginable as detailed as possible. It is truly a work of art and worthy of its own feature story. They too were victims of the “it’s just a pickup truck” numerous times during their build. Nothing stopped them from creating this masterpiece. If no-one else appreciated the level of detail and design that was put into this truck, well at least I do!
The custom mud truck I am building for my brother has taken on a life of its own. Just like water finds its way into tiny cracks, the anal and obsessive overlord in me found its way into this build.
Allow me to set the record straight and give you a little back story. I am by nature a ridiculous detail freak who knows only one speed. That speed is balls out, go big or go home, and no job too big or small, do it right or don’t do it at all. Unfortunately, my speed is also painstakingly slow while trying not to miss any details. So when my brother first approached me with this project, it was originally plain and simple. He had no budget. He wanted high horsepower, and it needed to go through the deepest of mud holes. I quickly did what I do, and made a list of parts and broke down the build into several mini projects that we would tackle one at a time. His first response was, “It is just a mud truck, it’s not one of your race cars!” I quickly forgave him because I know my little brother and he just didn’t know. What didn’t he know you may be asking?
Right off the bat as you probably have already surmised on your own, no budget and high horsepower do not go together. Neither does a custom suspension with 20” of lift with 50” tractor tires. Obviously my plan was to do all of the work myself saving him a fortune in labor, and any outsourcing I would need, I would barter with friends who were specialists where I am not. (machining, transmission, transfer case, and painting) My brother was fortunate enough to have his friend Steve help him with designing and fabricating the chassis. I am praying that this divide and conquer plan speeds up the process and allows me to focus on the drivetrain, plumbing, wiring, interior design and safety, painting, and final assembly.
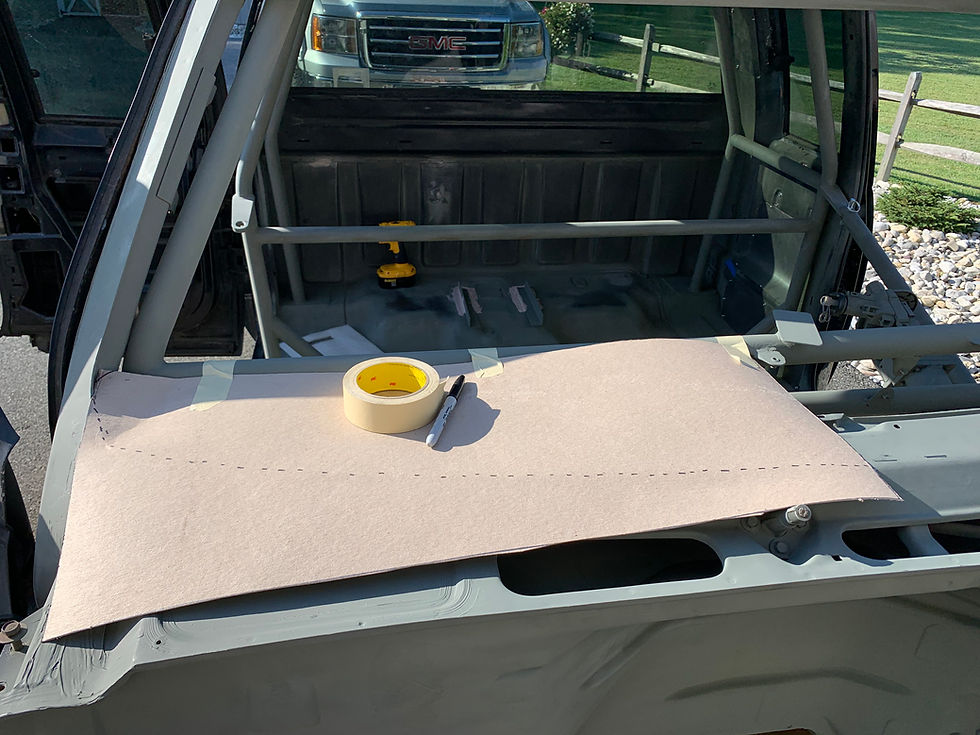
I know there are people who do this kind of stuff every day and are masters at bringing ideas to life with metal. I am not one of those people! I do however thoroughly enjoy the complete process of listening to the customer, seeing the design in my head, making templates, and creating something out of just an idea. This dash was certainly not needed for a mud truck but I had a blast making it a reality for my brother.

It’s just a mud truck, why do you need a dash? Well that’s what my brother wanted. Making the compound bends and matching the windshield radius to this piece of aluminum was not easy in my home shop. Seeing the smile on my brothers face when it was done was worth every drop of sweat.

The dash turned out great. I even convinced my brother into letting me get stainless steel, rounded head allen bolts to use as fasteners. That piece of angled metal in the center of the dash is the tachometer / shift light mount which was once again perfectly measured for my brother's comfort. He loved this idea until he saw that the tachometer was nearly $300. If he bails on the tach, it could be used as another towing anchor. I went a little overboard designing that.
My brother had a lot of basic questions about my plan and the list of parts I made. Questions like: Why do we need a $400 fuel pump? Answer – Because the engine we are building requires it. Why do we need -10 and -12 AN lines? Answer – Because the fuel pump and the engine require it. We are $1,000 into the fuel system I planned and that is not counting a custom fuel cell. (thankfully I have a brand new one that will work perfectly) After going over the complete parts list with him, he had a much better understanding of what he was getting himself into. I also had to educate him that normal, poor people like us, attack one project at a time as our budget dictates. This is why builds take years to complete.

My brother has some basic questions for me. Questions like, “how are you going to attach the dash to the cage?” “How are you going to make it removable in case I need to get under there?” Answer - We made some tabs and welded them into place using a homemade “placement jig” I made to ensure they are all in the same spot on the tube. As far as making it easily removable, I drilled them out and put my rivnut gun to good use so no one ever needs to get a wrench underneath the dash to take the bolts out.
It’s funny, when we were building the roll cage, he saw how time consuming each step was. (At least with me it is) When I finished welding in the A, B, and C pillar posts and plates, I told him I wanted to triangulate each one of them. His response, “What? We don’t need that! None of my friends have that!” I calmly responded, “the cage is useless without it. It is needed for the integrity of the entire cockpit. Safety first, and I only have one little brother.” He grumbled about how much extra work it would put on me and the extra steel and consumables it would take to finish. Yes, he was adamant about this build not costing me anything. He wanted to pay for the welding wire, nozzles, tips, gas, and any other tools we may need. Thankful for his concern and generosity, when he went back home, I compromised and added a triangle bar to the B – Pillar posts that are closest to his head. I still may add more, but let’s see if I win this battle first.

I strategically placed this bar here after doing all of the measuring, cutting, notching, and grinding to show him how easy it would be to simply weld in these bars. He agreed to let me put them on the B-Pillar posts. To win this battle I need to do all of the prep work without him watching.
My brother is a big boy and this fact was going to make certain decisions hyper critical. Decisions like finding the correct seat for him. The now famous, “it’s just a mud truck” was used a lot during decisions like this. As a matter of fact while I made him sit in one of my flat dining room chairs and measured his butt width, knee to knee span, shoulder width, and overall seat to head height, he repeated that phrase over and over. It took hours of research finding a seat that would fit him, and that he could afford. The same amount of work and planning went into finding the correct steering wheel, gauge and switch panel placement, shifter pedestal and location. Every aspect of this project was designed to fit him and fit him comfortably. Maybe people he knows never worried about things like this, and made stock parts work for them, but I don’t work that way. Having your cake and being able to eat it as well, is important to me. Why not be as comfortable as possible while enjoying your passion? Why not be as safe as possible while making a machine do things that will inevitably break them? I mean do you settle for just any chair to put in your living room so you could watch TV? No! You find the one that you melt into. Why should the decisions you make when building your dream ride be any different?

Here is the gauge cluster in design mode. The cardboard template proved itself worthy while making the transition to the aluminum.
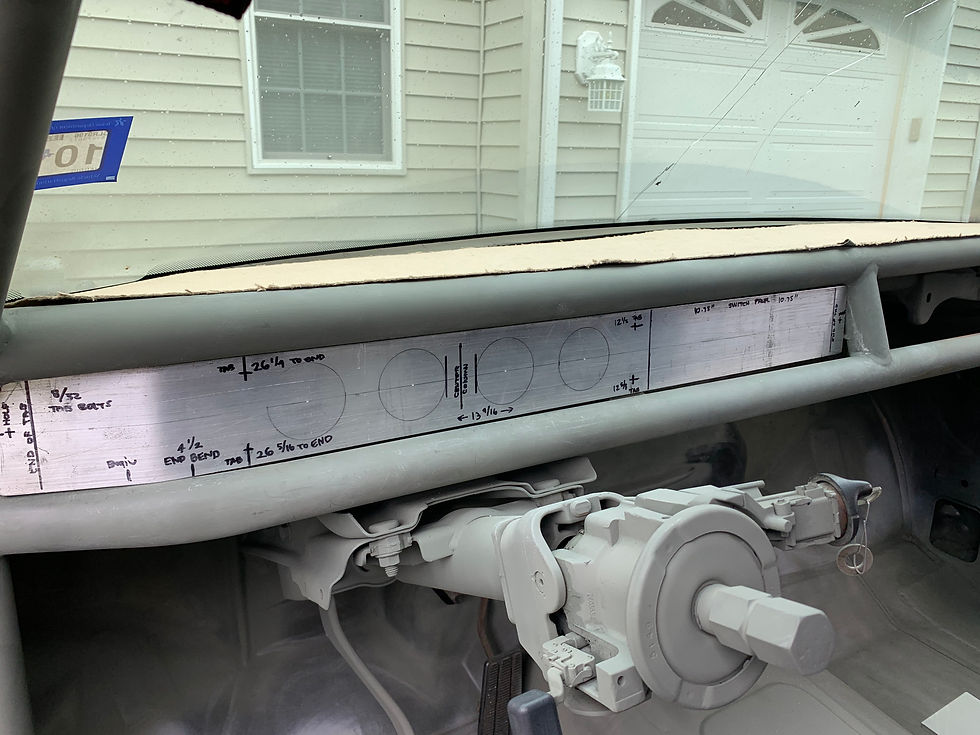
Listening to my brother on what he wants the gauge cluster to look like is one thing. Drawing it on paper and making a cardboard template is another thing. But seeing the actual piece of metal come to life is my reward every time. This gauge cluster will hold 4 gauges, an 8 circuit switch panel, and misc switches that are all perfectly measured for optimal visibility and comfort from the way he sits in his perfectly placed seat.
Friends, when I was building Big Red so many people came up to me and said, “it’s just a race car!” Is it me? Or is it a lazy world? I ask you all a question. Why can’t my race car be comfortable, and look like a show car at the same time? Why can’t I paint and detail every part underneath my car that no-one will ever see? Why can’t I take every possible step in reducing temperatures in coolant, fuel, and oils? Why did every one of my fasteners have to not only be of the highest grade and quality, but they all had to match? My simple answer is because it is mine! We are all unique and all have different tastes. When it comes to building a vehicle this should not be put to the wayside. In my opinion it should only get amplified and become an extension of who we are.
It’s not just a race car! It’s my car! Why can’t every fastener match? Why can’t everything be clean and polished? Why can’t a red motif be carried through the entire engine bay? So what there is more to keep clean. I enjoy keeping it looking new. Stop the hating and recognize we are all different. My likes don’t have to be yours and vice versa. Even underneath where no-one will ever see, I did not stop with going overboard on details. Sure the waterbox and/or traction compound make a mess under there, but like I mentioned before, It makes me happy and I enjoy cleaning.
So, to my brother, and everyone else who told me it’s just a mud truck, No it isn’t! First and most important, my brother is 50 years old and this has been a dream of his all of his life. He needs to realize that and so does everyone else. He is super passionate about mud trucks and the culture behind it. He deserves a dream come true for once in his life. Don’t we all? And lastly, it is no secret that I have issues. I admit to them and write about them every month. I like things detailed. I like things pretty. I like things overbuilt. This is who I am and it makes me happy. My own best buddy Shawn commented after I shared a picture with him of the shifter pedestal. “Is that a shifter pedestal or a tow bar? Your brother could put a tow strap around that and pull people out of holes.” It was funny and I took it as a compliment. But the fact is, I used materials I had laying around and wanted it to match the overall motif of the build which is, big, tough, bad-ass, and beautiful.
My brother wanted to sit as high as possible in that cockpit so he has complete visibility of all things in front him. Numerous measurements were taken in order to achieve this simple wish. Once the seat was chosen, the seat mount had to be made to get him to his desired height. What does that have to do with the shifter pedestal? I needed to get that shifter up high enough so my brothers arm made a comfortable 90 degrees when holding it. And yes, it did not need to be made out of the 1 5/8” rollcage tubing with ¼ steel plates. But it matches the overall theme of the build and it was material we had laying around. And……. One more anchor for towing is always a good thing.
What we do as gearheads with our machines is a form of art. What we do as builders is no different. Do us all a favor and quickly scold anyone that ever says, “it’s just a streetcar, an old hot rod, a race car, a drift car, a stock car, show car, or a mud truck.” Remind them it is not their car it is yours. Be yourself and be unique. Remember this, no one will ever be a better you than you!
Until next time
Keep Wrenching,
JT
Comments